
"In six months you won't recognize the UAZ"
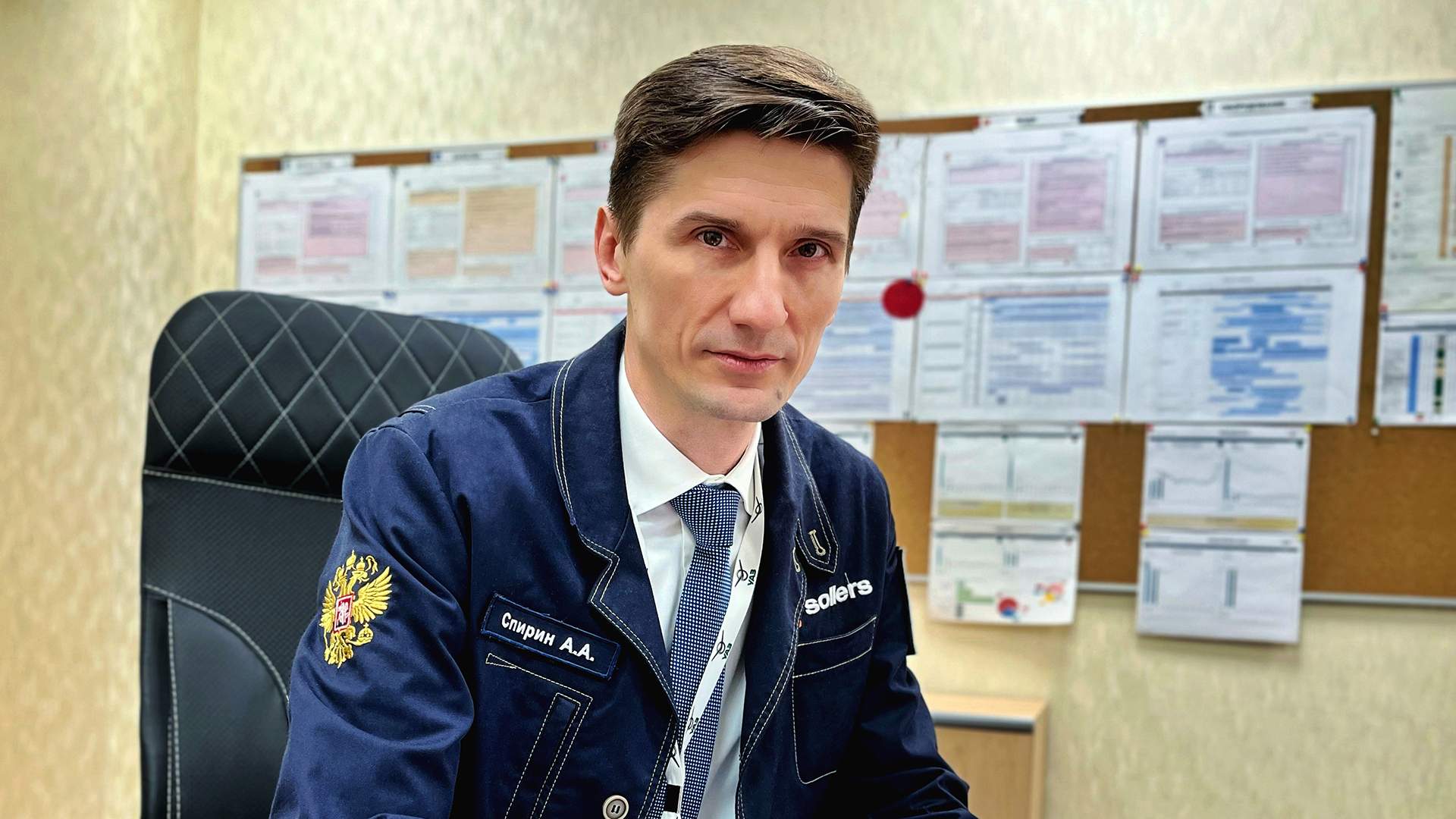
Production of several car models, including a new seven-seater SUV, will start at UAZ in the near future. In addition, the company will start producing additional types of components, including passive safety elements of the machine. But long—standing and well—known representatives of the current model range - "Hunters", "Loaves" and "Patriots" - also do not plan to be removed from the assembly line, on the contrary, serious modernization awaits them. Alexey Spirin, CEO of the Ulyanovsk Automobile Plant, told about this and not only in an exclusive interview with Izvestia.
"UAZ is undergoing the most significant transformations in its entire history"
— You came to UAZ in 2019. Prior to that, they had worked for a long time in a joint venture with Ford, Renault and Toyota. Is the experience of working in foreign car companies helping now?
— Of course! The importance of work experience in companies representing the global automotive industry cannot be overestimated. He taught us to be demanding of ourselves first of all, to react quickly to any difficulties, and allowed us to feel the spirit and rhythm of large-scale production. And one of my main production tasks is to try to convey to the employees that the provision of the main conveyor depends on each person in the enterprise. The practice of building a production model in which each employee knows his function and tries to avoid downtime has been applied here, at the Ulyanovsk Automobile Plant.
I have been working at Sollers since 2008. In 2019, he was appointed Executive Director of UAZ. On the one hand, the factory is close to the start of my career at AVTOVAZ in 1999. The factories in Tolyatti and Ulyanovsk are very similar in terms of staff, technology, and many approaches to work. On the other hand, it already required further development of the production system, the introduction and "polishing" of modern production standards, which I met while working in foreign car companies.
— From the outside, all car factories are about the same. What is the difference between UAZ and the companies where you worked before?
—— First of all, deeper production technologies. That is, in addition to welding, painting, assembly, and production of special vehicles, there is a press shop, its own metallurgy, its own forge, and the production of automotive components. Therefore, a wider range of knowledge is required here. Again, the staff is many times larger than at most enterprises where I worked before. In addition, since UAZ is an integral part of one of Russia's largest automakers, it is very important to understand not only the macroeconomics of the plant itself, but also its impact on the company's business as a whole.
— How has the Ulyanovsk Automobile Plant changed over the years of your work, and what have you personally managed to change? What ideas and projects are you planning to implement?
— The Ulyanovsk Automobile Plant is currently undergoing perhaps the most significant transformations in the entire history of its existence. We are actively working to transform the production site into a modern industrial park specializing in the production of frame construction vehicles and automotive components, with new production facilities and technologies. Come to us in the middle of this year — you won't recognize the UAZ. The number of new production facilities that have already been created or will be launched on the territory in the very near future will significantly transform the site. Including through the implementation of new projects related to the launch of the Sollers line.
For example, over the past two years, a new Sollers Cargo building has been opened here in Ulyanovsk, where Sollers Argo light commercial trucks have been manufactured, and Sollers TR medium-duty trucks have also been launched. In deep synergy with the production of UAZ, the project of assembling Sollers ST6 and ST8 pickups using full-cycle technology has been implemented. By the end of the year, another model, the Sollers ST9, will be on the assembly line. It is important to note that we are not following the path of large-scale assembly, which is often referred to as re-gluing the nameplate. We are modernizing the production base and organizing localized production, from welding and painting bodies to installing diesel engines manufactured at the Sollers plant in Yelabuga and gearboxes manufactured at the Zavolzhsky Motor Plant in the Nizhny Novgorod region. All the changes are fundamentally changing the very culture of UAZ car production. As the machines themselves change, so does the approach of the people who produce them. We see the fire in the eyes, the attitude towards the car on the assembly line as something of our own, native. Believe me, this is very important, it brings the team together.
Our plans include further deepening of localization in terms of stamping, which will require renovation of the pressing equipment and new stamping equipment. Also, this year, the production of passive safety systems, electronics and other important components of the car will be launched, some of which will be produced here, at the UAZ site.
— Do I understand correctly that you intend to provide yourself with the necessary components, assemblies and assemblies to the maximum?
— Yes, import substitution is one of our priorities. Moreover, not only by switching to local components from third-party manufacturers, but also by creating our own production facilities for key components and assemblies within the company. Let's remember 2022, when foreign automakers, as well as manufacturers of components and components, left, slamming the door. Then Russian car factories faced a dilemma — to stop production for a while or to quickly look for new solutions. We went the second way.
Of course, it was necessary to significantly simplify the design of cars — for this purpose, the government of the Russian Federation introduced temporary breaks in technical regulations for all Russian automakers. But I want to emphasize that the UAZ conveyor did not stop for a single day. This was made possible due to the very high degree of localization of the machines. The transition to affordable imported technical solutions dictated the need to quickly adapt production to the sanctions realities. It was a strenuous job that doesn't stop today. It is important that we were able to quickly find alternative options. One example is the engine control units that became unavailable at one point, and we replaced them with domestic analogues as soon as possible.
Some solutions have not passed the test of time, and we have abandoned them. Other proven solutions were from the past, and we immediately realized that they were temporary. Together with suppliers, we have improved the components and components, and today the car already has an anti-lock system, domestic engine control units, and much more. Some solutions have been changed or significantly improved. For example, a manual transmission: today this unit is no longer the same as in 2022-2023, it has been thoroughly modified. The same can be said about the transfer case.
All this required a significant upgrade of our equipment fleet, and we are currently implementing a major investment program in the machining industry. This gives us an improvement in the parameters and quality of a node. We are gradually moving to the Russian component base. Already, a significant part of the components on UAZ vehicles are of our own production. And their range will only expand.
I have already said that this year we will start production of passive safety elements at the UAZ site. I'm focusing on: This is not just an assembly, but a full-fledged production "from raw materials", starting with casting the steering wheel frame from magnesium alloy to sewing the airbags themselves and producing control units. Production will be organized here in Ulyanovsk, literally in the neighboring building of the enterprise. The necessary equipment is already being imported and installed there. If we go through the composition of the car, then almost every element has its own work going on — this applies to both key elements, such as engine control units, and components such as electrical wiring, pipes, and even fasteners. As a result, if the localization of our models was about 80-85% before 2022, now the level reaches 95-96%.
"We will launch production of a new seven-seater SUV at the UAZ site"
— Not so long ago, UAZ began production of light trucks and pickups under the Sollers brand. What did this give to UAZ itself and those models that are traditionally produced at the enterprise?
— All the models that are currently being produced at the Ulyanovsk Automobile Plant, and will also be produced in the future, are united by a common genetics — these are frame cars. And with the exception of some light and medium—duty trucks, of course, there are also four-wheel drive. When working on new projects, we primarily apply technical solutions to the entire model range of the Sollers and UAZ brands. For example, a diesel engine combined with a six-speed gearbox, the production of which has been mastered at the enterprises of the Sollers group in Yelabuga and the Volga region. This power unit is installed on Sollers Argo trucks, Sollers ST6 and ST8 pickups. We will use the same combination of engine and transmission in the updated UAZ model range. The first to receive it is the commercial model UAZ "Profi", and then the "Patriot". We expect to bring them to the market in the second and fourth quarters of this year, respectively. If we talk about the development of the site as a whole, then the main task is to create a full—fledged industrial park at the Ulyanovsk Automobile Plant. And this, in turn, implies the improvement of technologies, because new equipment is being purchased for new projects and existing equipment is being upgraded. This applies to welding, painting, and integration with IT systems. All this has a cumulative effect on the entire product range.
— Can you give examples of such influence?
— For example, at the end of January, a new robotic equipment for applying primer was introduced in the paint shop at the enterprise. The bodies of the entire UAZ model range and Sollers pickups pass through it. This makes it possible to significantly improve the quality of the preparation of the body for the application of the enamel itself, which, of course, has a positive effect on the quality of the final painting of absolutely all machines coming off the assembly line. Recently, a new robotic complex was introduced at the welding site. The equipment has a higher accuracy and speed of operation, while providing a more reliable articulation of the elements. And this work is carried out daily.
— As part of the integration with foreign partners, are there any plans to create your own new car models?
— Of course, there are such plans. Moreover, such work is already underway. For example, we are planning to launch production of a new seven-seat frame SUV on the site soon. This will be a model developed by Sollers specialists on the wheelbase of a pickup truck. We plan that the production of the car will begin in Ulyanovsk at the site of the industrial park at the beginning of next year. But let's be patient.: as soon as there is news about this project, you will definitely find out.
If we talk about the UAZ model, then at the end of the year we will present an updated version of our flagship model, the Patriot. It will still remain a full-fledged SUV, only with modern options and more adapted for comfortable operation. In other words, the emphasis will be on the stylistic component and practicality. Overall, we have big plans to update the current model range. This is a necessary evolution. We're talking about technology — the gearbox, the handout, passive safety—as well as aesthetics: modern LED optics, interior elements, and exterior details. In any case, the brand's genetics are preserved now and will be preserved in the future.
— On the basis of UAZ, third-party manufacturers make various special modifications: tank cars, utility vehicles. Why doesn't the factory produce such versions?
— The plant produces mass-produced special versions, for example, cars for law enforcement agencies, orders for which are confirmed in volume and have standard requirements. Small—scale production is a completely different approach to business, even individual in some ways. For example, in different cities, the requirements for municipal equipment may differ due to the peculiarities of the climate and terrain. That is why UAZ cooperates with partners for whom such a business is relevant. We supply the basic chassis taking into account certain requirements, and our colleagues work individually with the customer. This is an established practice in the automotive industry.
"There is a steady demand for the Loaf, so it will remain on the UAZ assembly line."
— Does the expansion of the model range of cars produced at UAZ mean the gradual abandonment of some old-time models? For example, the same "Loaf" has been allowed in for 67 years. What is her fate?
— These processes have nothing to do with each other. The expansion and appearance of new models does not come at the expense of those already being produced. Each car has its own customer. Both Loaf and Hunter have it: these machines are in demand, they are needed. And as long as there is demand for them, the plant will produce them — this is the law of the market. Again, the same UAZ-469 has changed a lot: for example, the engine originally had a capacity of 70-80 horsepower, now it has 150. The suspension has been upgraded, and additional safety features have been added. During their production life, these vehicles have complemented their military use to civilian ones in various industries: now they are in demand in agriculture, oil and gas production, utilities and service services, especially in remote regions of the country with poor roads or where there are no roads at all.
The Loaf is a unique off-road vehicle, extremely simple, maintainable in the field, and inexpensive to operate. In the right hands, he is a hard worker, a warrior, a builder, and a doctor. It is not for nothing that UAZ was awarded the Order of the Red Banner of Labor for the development and implementation of our classics in production. There is a steady demand for this model, so it will remain on the UAZ assembly line.
— Speaking of the "military" roots of the Ulyanovsk models... It is no secret that UAZ cars are actively used by our soldiers during a special military operation. Do you have any suggestions from them? Do I have to change something in the cars?
— Our specialists — engineers, technologists — are constantly in the free zone and, in fact, receive real-time feedback from the fighters. I myself regularly visit military formations, meet with unit commanders, listen to their wishes and comments, including criticism. I see with my own eyes that the operating conditions of cars in the SVO area are very specific and extremely difficult, in some cases they exceed the most difficult test tests that cars undergo before starting production. And the real feedback from those who operate them there gives us a lot of experience and understanding of what needs to be changed or improved in a particular model. After all, not only the fulfillment of a combat mission depends on the reliability of the machine, but also the lives of people.
Of course, there are specific requests and requests, such as protection from drones or electronic warfare, which we carry out. It is clear that in "civilian" operation they are not required on cars. But many changes that will be useful and important in peaceful life have already been implemented on production machines. For example, based on feedback from its participants, the bridges were upgraded: we introduced additional seals sealing the crankcase of the car's bridge, and moved the breather from the axle housing above to the housing of the crankcase itself. This dramatically reduced the risk of moisture entering the gearbox. Yes, this is a certain increase in price, which has a slight effect on the price. But it is incommensurable with how such modernization affects the resource and reliability of the bridges themselves, and even in conditions where routine maintenance is difficult. Reinforced crosspieces, modified driveshafts were also introduced, and the rear suspension was upgraded.
UAZ is the most affordable product in its segment"
— At the very beginning of our conversation, you talked about the imminent appearance of diesel versions of the "Pro" and "Patriot". What is the reason for the decision to bring modifications based on this fuel back to the market? How much of the sales share can they take?
— This, like any of our decisions, is primarily driven by market requirements. If we talk about the "One-and-a-half truck", now in our country the pool of commercial vehicles is formed mainly by diesel cars. The advantages are obvious: high efficiency, a serious power reserve and impressive traction during acceleration, while diesel modifications are comparable to gasoline versions in terms of maintenance intervals and maintenance costs. There is a steady demand for such models, and they will occupy their niche in the market. We expect that they will account for about half of Pro's sales in the future.
The motivation for the Patriot is different: we see that all full-size SUVs have diesel versions, and we understand that such a modification is necessary for the flagship model of the UAZ brand. We already have several prototype vehicles equipped with a diesel engine and a six-speed manual transmission. They are currently being tested. We plan to start mass production and launch them on the market by the end of autumn.
— And what will happen to the prices of diesel "UAZ"?
— I would not like to get ahead of myself. Regarding the "Pros" so far, I can say that the cost of the diesel version will obviously be slightly higher than the gasoline version. But at the same time, such a car will still be much cheaper than its closest competitors. At the same time, according to our calculations, all its advantages will make it possible to compensate for the difference in price relative to the gasoline version in one and a half to two years of ownership.
As for the diesel Patriot, it's too early to talk about the price at this stage. It should be understood that, in addition to the engine and gearbox, the car will receive a new electromechanical "distributor". The flagship will get LED optics, a new multimedia system and an updated interior. We expect that the share of diesel-powered modifications in the total sales volume of UAZ Patriot will be 15-20%. Therefore, we will try to set such a price to ensure these indicators.
— Until 2022, there was a version with an automatic transmission in the UAZ Patriot line. The reasons for her disappearance are clear. But there have already been official announcements of the return of this type of gearbox to the model range. At what stage is the issue of this promising option and can we expect it to appear on other models, for example, on the same "Pro"?
— Yes, there are indeed plans to introduce this type of transmission in the UAZ model range. The possibility of equipping a commercial "Pro" with an automatic transmission is also being considered. But the implementation of any unit is a rather lengthy process that requires a meticulous approach. After all, choosing a transmission that meets certain technical specifications and layout solutions is only half the battle. It is also necessary to combine the units, adapt, test, test, certify them, and this takes time. Right now, we are fully focused primarily on updating the model range. Let's return to the issue of the automatic transmission later, after the launch of planned updates in 2025.
— Over the past two or three years, prices for new cars have increased significantly. And UAZ is no exception. What is the reason for this?
— Prices for new UAZ cars increased by 6% last year. This is significantly lower than the official data on inflation in Russia. Of course, there are macroeconomics, production costs, which are influenced by tariffs on resources, and the sharply increased costs of logistics, raw materials, and components. Against this background, we strive to actively reduce our own costs so as not to pass these costs on to the consumer. I can say with confidence that at the moment UAZ remains the most affordable product in its segment.
Переведено сервисом «Яндекс Переводчик»